The legendary 7.3 Power Stroke Diesel engine, when properly maintained can provide years of trouble…
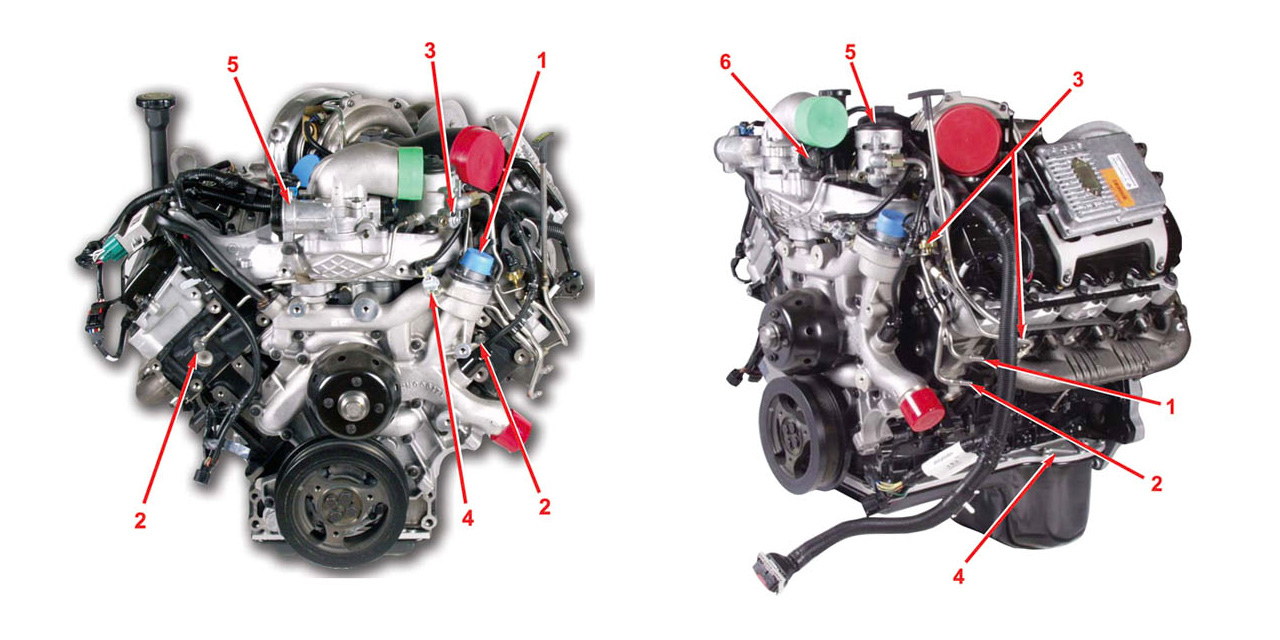
Powerstroke History-6.0L
As is typical in the world of automakers, planning for a whole new engine begins years before it ever debuts. Case in point, Ford and Navistar began development on the 6.0L Power Stroke in the late ‘90s, right in the thick of the 7.3L’s production heyday. The reason? Significantly more stringent NOx emission standards were fast-approaching for diesels and both companies realized a brand-new engine platform was the only way to meet them. So before you ask why they killed the 7.3L, here’s your answer: emissions. Not only would the 7.3L Power Stroke’s life have been shortened by being saddled with exhaust gas recirculation, but the most powerful 7.3L Navistar ever produced checked in at 275hp. By comparison, GM’s LB7 Duramax and the 5.9L common-rail Cummins powering Dodge Rams were already up to 300hp or more. Long story short, Ford had a legal requirement to meet and a truck war to win—and the 7.3L wouldn’t have worked.
Making the 7.3L appear ancient in nearly every way, the 6.0L Power Stroke featured four-valve cylinder heads, a quick-spooling variable geometry turbocharger, a lower voltage yet higher-pressure version of the HEUI injection system and a crankcase bed plate for superb bottom end strength. In time, some of these newfangled features proved troublesome as EGR, head gasket, oil cooler, high-pressure oil and sticking turbo issues mounted. On the upside, the stout short-block proved durable, the added engine power and responsiveness was appreciated by both heavy-haulers and hot-rodders alike and the 5R110 automatic transmission option was lauded for its efficient operation and ability to handle huge torque input.
Our Take on the 6.0L Power Stroke
From people both inside and outside of the diesel industry, the 6.0L tends to get a bad wrap. In some instances, this is warranted. In others, not so much. In our opinion, maintenance is key if you want this engine to last. It can’t be neglected like the 7.3L can and still give you years of loyal service. It’s not a Duramax and it’s certainly not a Cummins, but if it’s taken care of and upgraded in the appropriate areas the 6.0L can be just as reliable. No matter your position, it’s still more cost-effective to own a 6.0L than its direct successor: the 6.4L. We’ll dissect that engine next.
6.0L Hard Facts
Production: | 2003 to 2007 | Valvetrain: | OHV, four valves per cylinder, single cam |
---|---|---|---|
Bore: | 3.74 inches | Injection System: | Siemens high-pressure oil, direct injection |
Stroke: | 4.13 inches | Injectors: | Siemens hydraulically actuated, electronically controlled (under valve cover) |
Displacement: | 365 ci | High-Pressure Oil Pump: | Siemens swash plate, axial-piston pump |
Compression Ratio: | 18.0:1 | Turbocharger: | Garrett Variable geometry GT3788VA |
Block: | Cast-iron | Intercooler: | Air-to-air |
Rods: | Powdered-metal | Emissions: | Exhaust gas recirculation (EGR) |
Pistons: | Cast-aluminum | Horsepower: | 325hp at 3,300 rpm |
Heads: | Cast-iron with four 14mm head bolts per cylinder (with sharing) | Torque: | 560 lb-ft at 2,000 rpm (’03-‘04) to 570 lb-ft at 2,000 rpm (’05-‘07) |
Modernized Engine, Mass Production
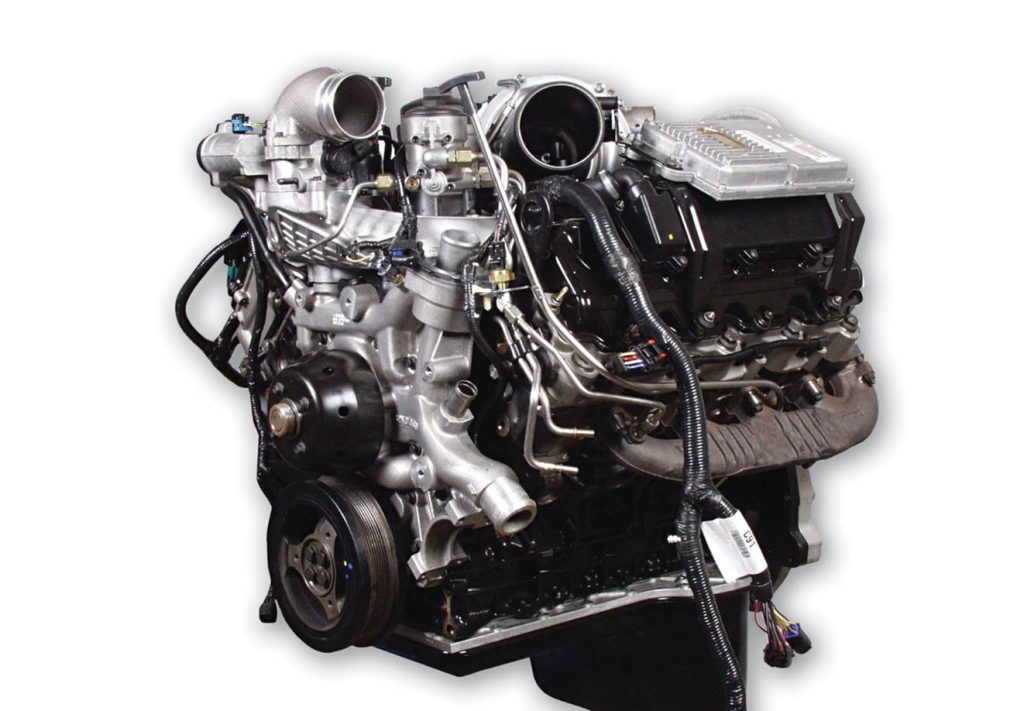
By releasing the 6.0L Power Stroke for the 2003 model year, Ford was able to meet the 2004 emissions deadline an entire year in advance. One of the key elements in adhering to the new regulations was the engine’s employment of an exhaust gas recirculation system. Thanks to the success of the 7.3L Power Stroke, Ford’s Super Duty trucks were outselling the competition by huge margins—a trend that continued when the cleaner, more powerful 6.0L came along. In fact, midway through the 6.0L’s production run, some two million engines were predicted to be manufactured between Navistar’s plants in Indianapolis and Huntsville, Alabama.
New Design, Stronger Rotating Assembly
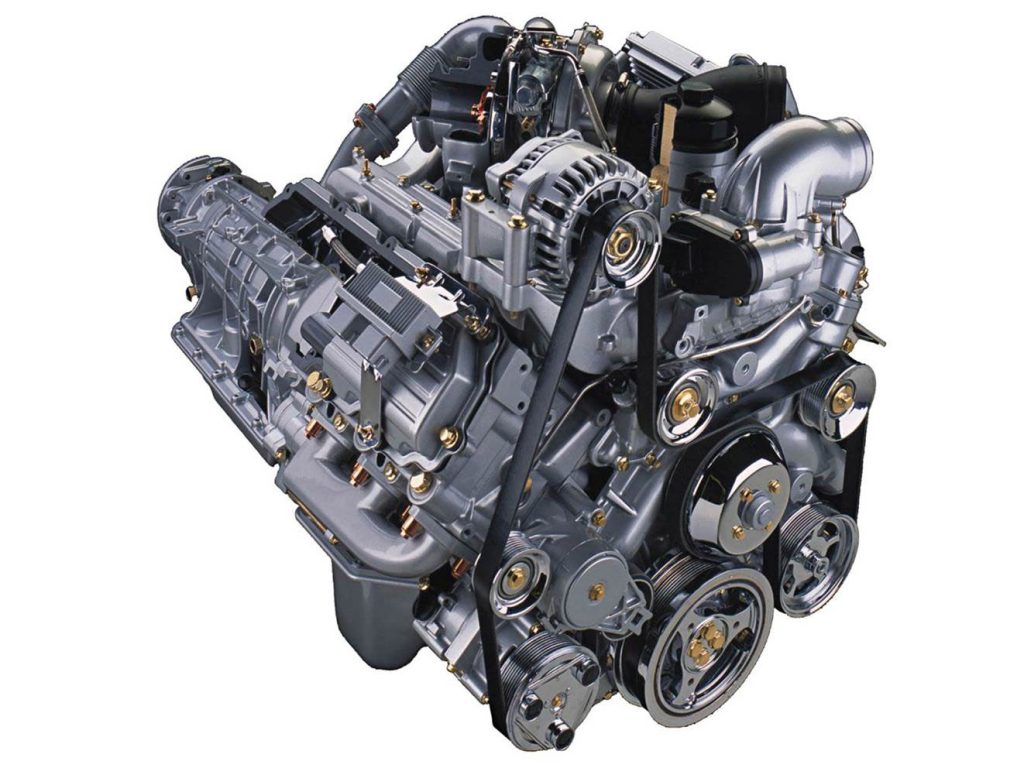
With both its oil cooler and high-pressure oil pump integrated into the block, the 6.0L was a more compact package than the 7.3L had been. Also different from the 7.3L, the gear train for the crankshaft, camshaft and high-pressure oil pump were relocated to the rear of the engine. Bottom-end strengthening came in the form of the crankshaft’s main and rod bearing surfaces being treated to induction-hardening and the crankshaft being anchored in place via a bed plate (no main caps to walk around).
Torque-to-Yield Head Bolts
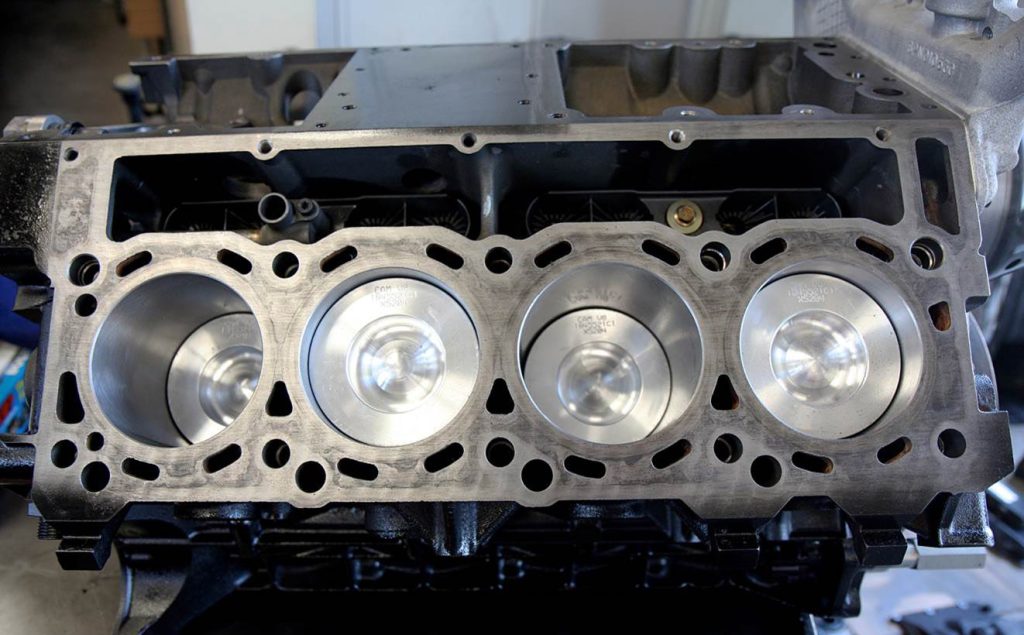
Nearly everyone knows that 6.0Ls are notorious for blowing head gaskets, but why is this particular failure so prevalent? Many factors can contribute to a blown head gasket, but it all starts with the head bolts—the type and the lack of them. Torque-to-yield head bolts are nothing new in automotive engines, but once a TTY fastener stretches beyond its yield point, it becomes permanently elongated. This translates into a loss of clamping force. The 6.0L’s design employs just four TTY head bolts per cylinder (the 7.3L utilized six per cylinder). The head bolts might measure 14mm in diameter, but there simply aren’t enough of them to contend with the cylinder pressure being created beneath them. If a 6.0L is left untouched, the head gaskets can live quite a while, but once modified it doesn’t take long to pop one.
Powdered-Metal Rods
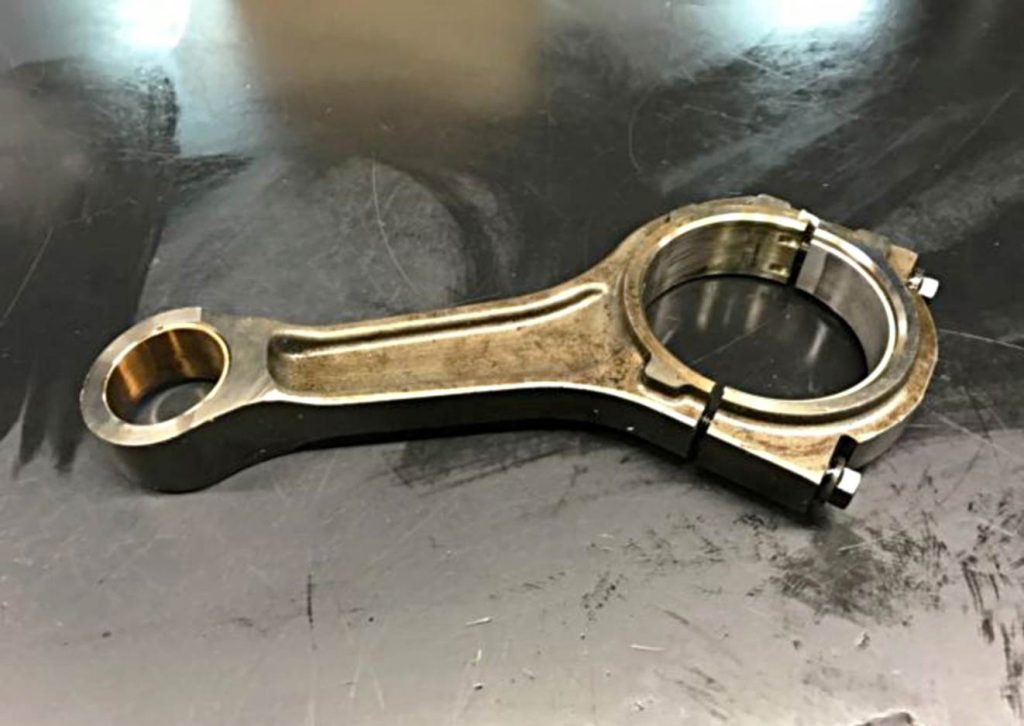
Despite powdered-metal connecting rods getting a bad name with the 7.3L Power Stroke, the units used in the 6.0L are some of the strongest OE rods we’ve seen in a diesel. Granted, the 6.0L’s revvy, high-rpm nature tends to keep the rods from being exposed to excessive torque, but they’ve more than proven their durability in both high horsepower and high-mile applications. In the diesel aftermarket, the 6.0L’s rods are known to handle 700rwhp (1,200 to 1,300 lb-ft of torque).
Four-Valve, High-Flow Cylinder Heads
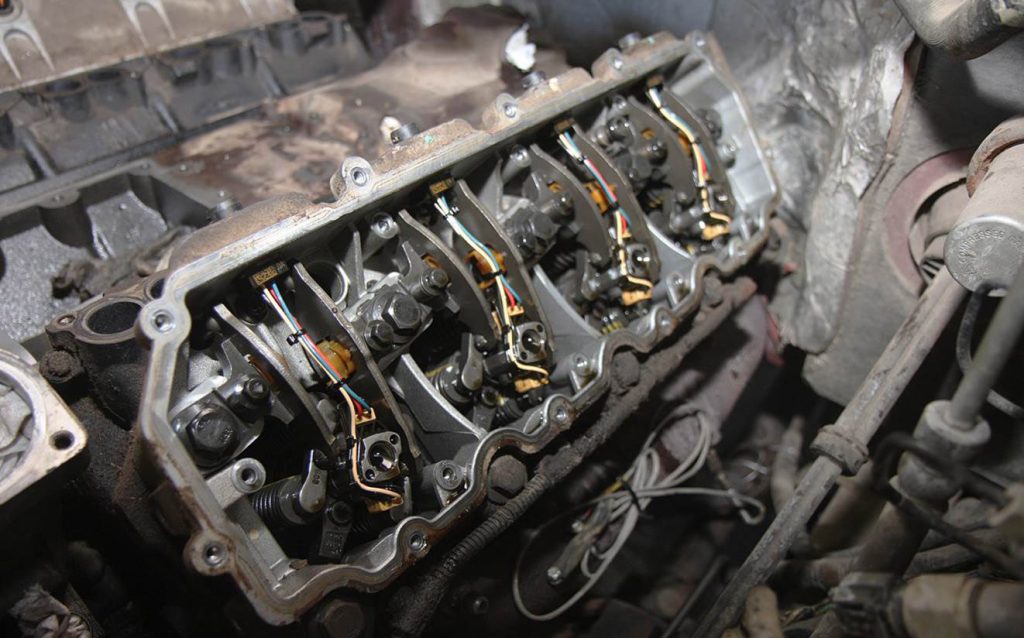
With four overhead valves per cylinder, the 6.0L cylinder heads flow considerably more air than the two-valve heads found on the 7.3L. An aluminum rocker box mounts to the top of each head and fastens in place courtesy of the head bolts. In addition, the rocker box provides the mounting point for all of the rocker arm fulcrums and provides the connector pass-through ports for the injector and glow plugs.
Rear-Mounted HPOP
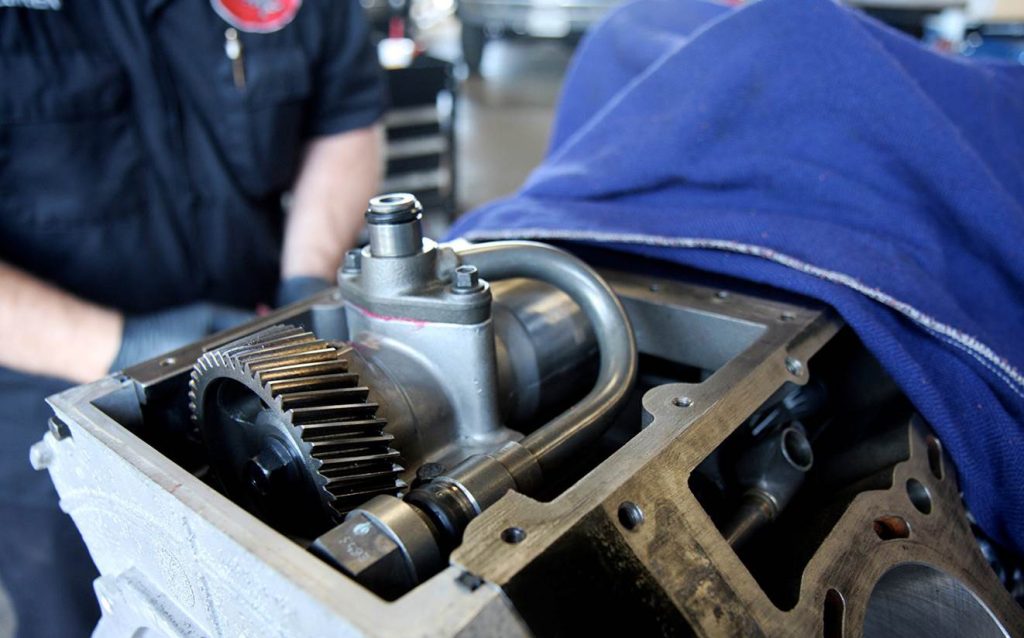
Like the 7.3L Power Stroke, the 6.0L relies on highly pressurized engine oil to actuate the fuel side of its injectors. All of that starts here, with the swash-plate style high-pressure oil pump (HPOP) sending the required oil volume through the rails. However, on the 6.0L the HPOP is located at the rear of the engine, buried under the HPOP cover and turbocharger. Its location makes it a fairly laborious endeavor to address failures—and unfortunately failure ran rampant on the 6.0L’s HPOP (especially on the early ’03 units).
The “Long-Crank, No Start” Culprit
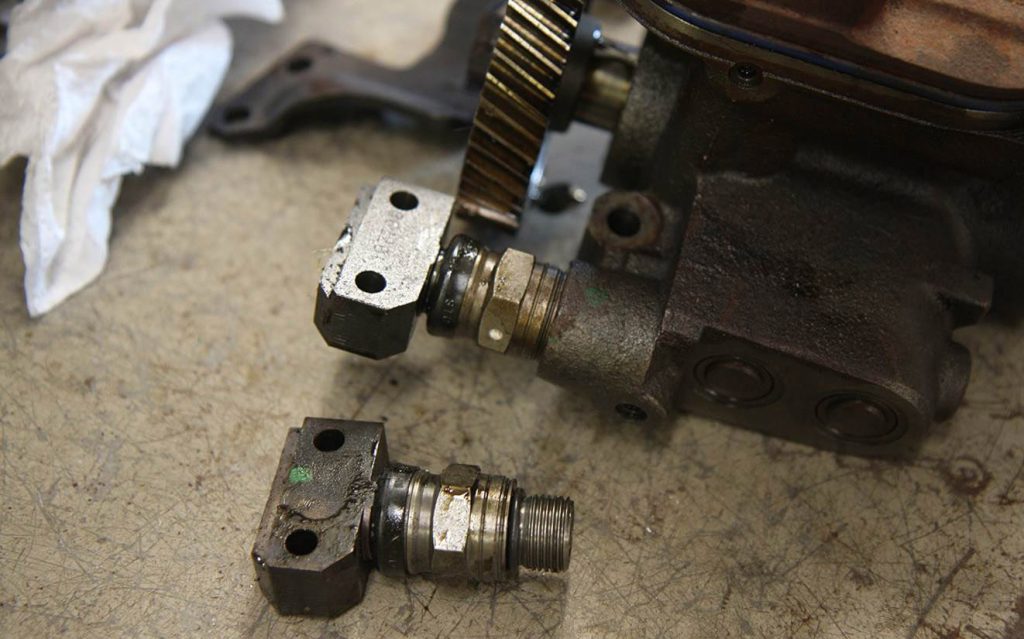
While a host of issues plague the 6.0L’s high-pressure oil system (namely leaks), this one is perhaps the most notorious. On ’04.5-’07 engines, the seal within the snap-to-connect (STC) fitting that attaches the branch tubes to the high-pressure oil pump is prone to wear and eventually fails. When the engine is warm and the oil is thin, the system can’t build enough injection control pressure (high-pressure oil pressure) to fire up again, causing a “long crank, no start” scenario to unfold. When the engine is cold and the oil is thick, adequate ICP can be built and the engine will usually fire right off. A threaded fitting was used on ’03 to ’04 models, so it wasn’t a problem on earlier engines.
Gen II HEUI Injectors
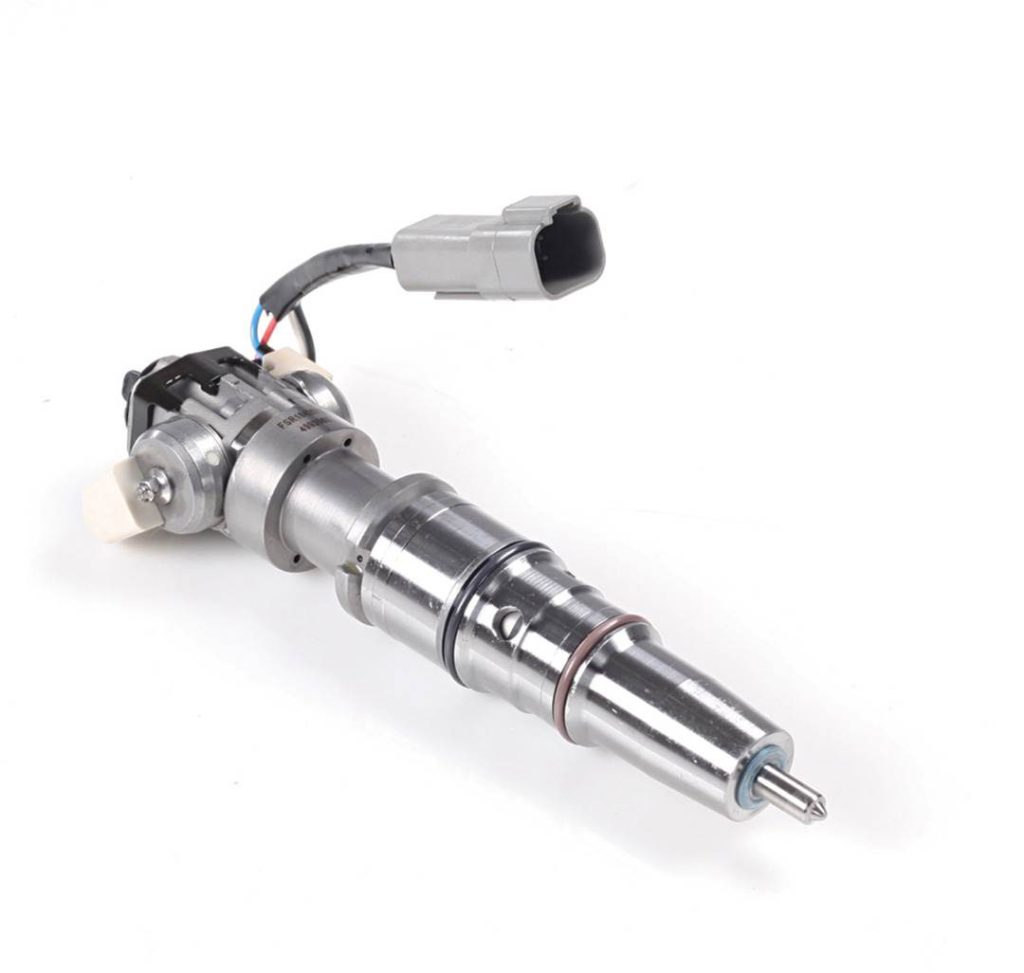
The injectors used in the 6.0L’s second-generation HEUI injection system (though technically not called HEUI on account of that being a CAT acronym) were supplied by Siemens, but utilize digital valve technology licensed from Sturman Engine Systems. Similar to the 7.3L injectors, they depend on high-pressure oil to actuate the fuel side of the injector. The oil—pressurized as high as 3,600 psi—enters the injector through the spool valve (a poppet valve performs this function in the 7.3L injector), which is opened via a 48-volt, 20-amp coil and closed by a second coil on the opposing side. With the higher 3,600-psi injection control pressure seen in the 6.0L (and with the oil-to-fuel pressure effectively being multiplied seven-fold at the nozzle), in-cylinder fuel injection pressure can reach 26,000 psi. The additional pressure over what the 7.3L produced (21,000 psi) is a big reason why the 6.0L emitted less particulate matter and made more horsepower and torque.
FICM Replaces the IDM
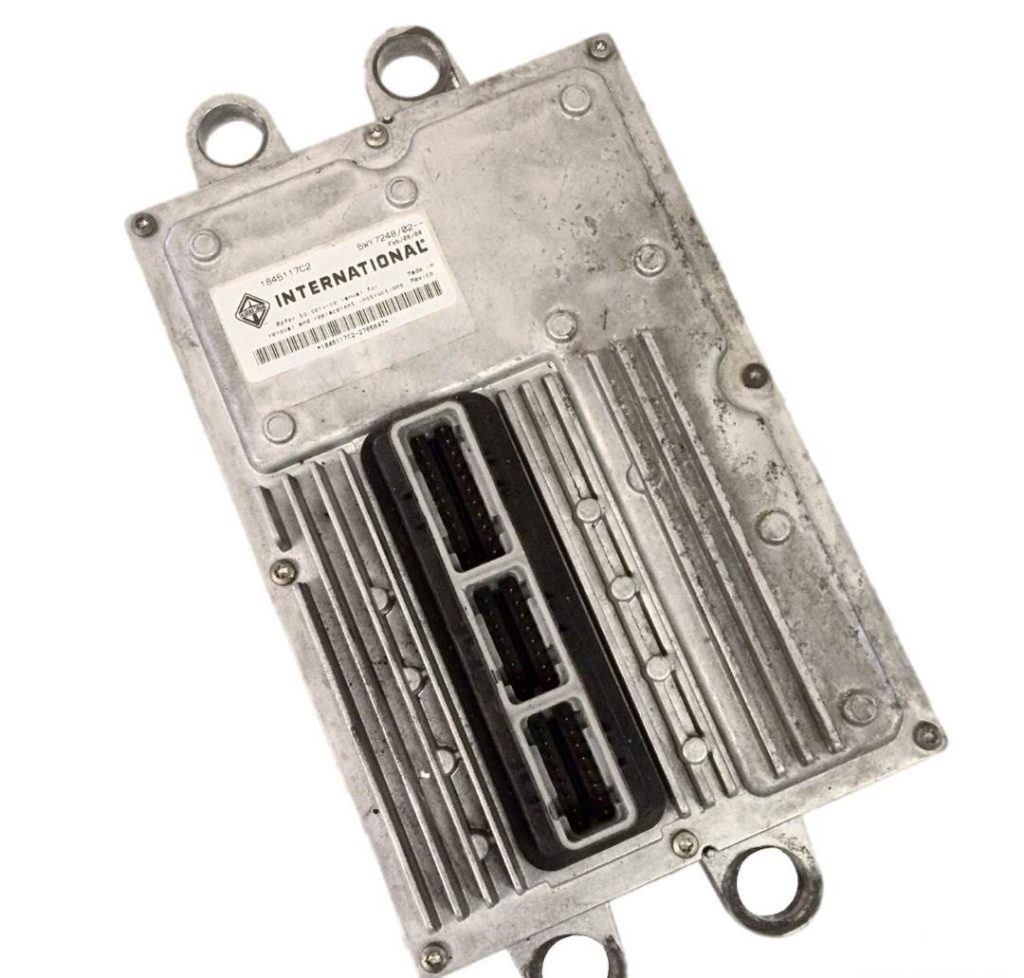
Assuming the job of the IDM on the 7.3L but carrying out the same task, the fuel injection control module (FICM) is responsible for energizing the injectors on the 6.0L (i.e. opening and closing the aforementioned spool valves). When commanded by the powertrain control module (PCM) via CAN bus, the FICM sends a 48-volt pulse to each injector, down from the 100-to-120-volt pulse used on the 7.3L. However, unlike the 7.3L’s IDM the FICM would prove to be a rather fragile piece. Dying batteries can lower the voltage output of the FICM to a point where engine performance suffers tremendously and the driver side of the module is permanently damaged.
The Domino Effect Begins at the Oil Cooler
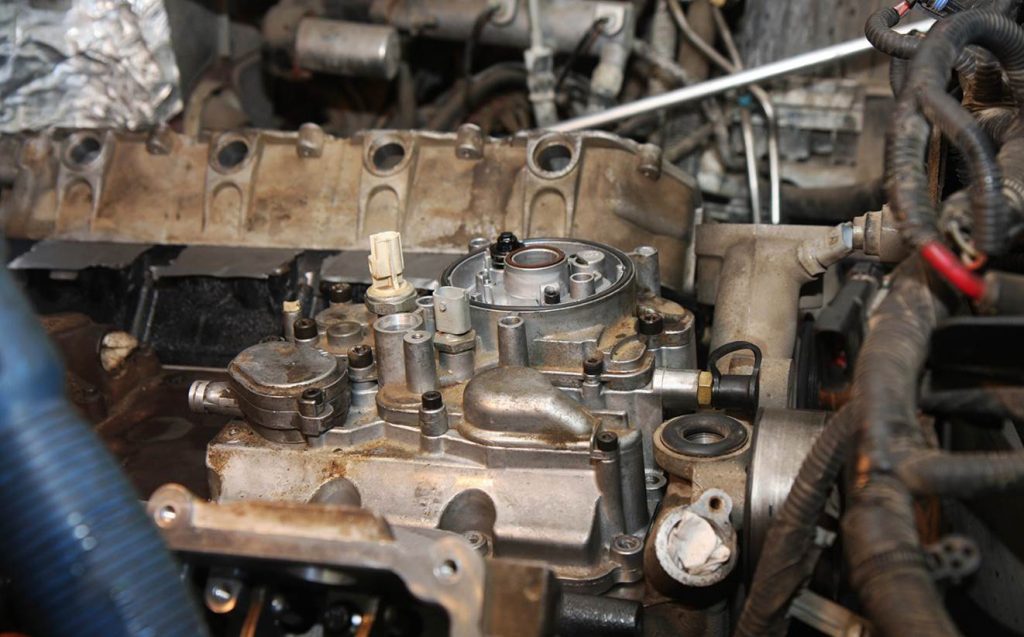
Located at the front of the lifter valley and integrated into the block itself, the 6.0L’s oil cooler is arguably its biggest shortcoming. The tiny coolant passageways within the stacked-plate heat exchanger are prone to plugging up with casting sand, suspended solids in the coolant itself and other debris. Eventually this lack of coolant flow causes engine oil temperature to skyrocket—the same oil that’s being supplied to the HPOP and used to fire the injectors, along with lubricating the bottom end, valvetrain and the turbocharger. Compounding the problem, a plugged oil cooler also starves the EGR cooler of the vital coolant it needs to effectively lower the extreme exhaust gas temperatures it sees. If gone unnoticed, the EGR cooler will eventually overheat and burst. More than 90 percent of all the 6.0L’s infamous EGR cooler failures occur because of a plugged oil cooler.
Oil Cooler Insurance
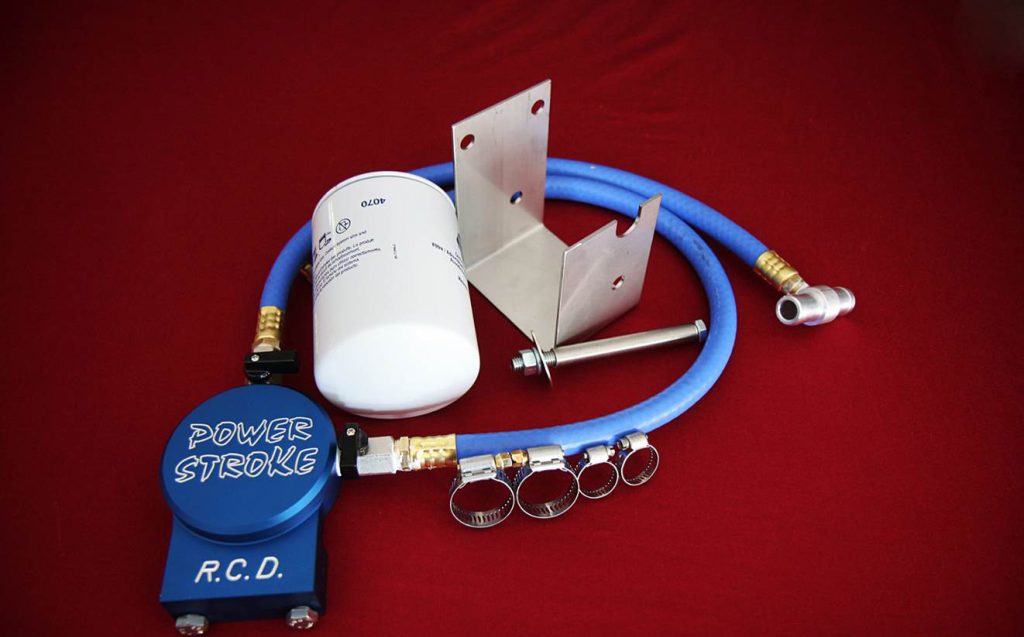
Shockingly, because of cooling system contaminants the average 6.0L oil cooler only operates unimpeded for 50,000 miles. To cleanse the coolant circuit of any oil cooler-clogging debris, this is one of the best bolt-ons you can add to your 6.0L. Called a coolant filtration system, they’re widely available in the aftermarket, run between $150 to $200 and filter engine coolant in a bypass manner using a spin-on filter with a 2-10 micron rating.
EGR Introduced
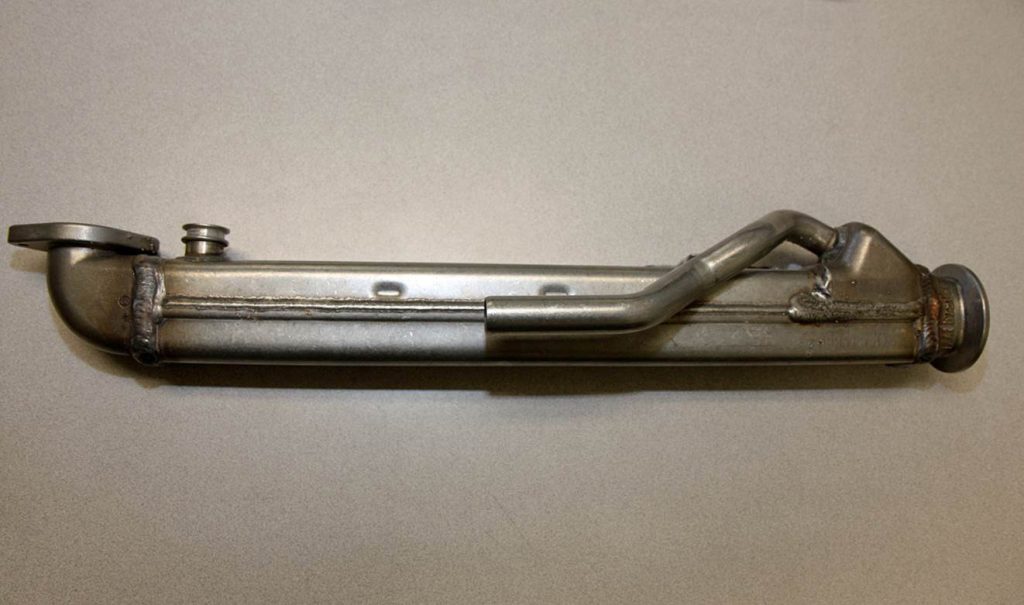
To curb NOx emissions, exhaust gas recirculation (EGR) is employed on the 6.0L. As is common on V8 diesels, exhaust gasses are routed into the EGR cooler from the passenger side turbo up-pipe. Inside the cooler, exhaust flows through metal tubes surround by engine coolant and within a span of less than 12 inches exhaust gas temperatures can drop as much as 700 degrees F. Common issues with the 6.0L’s EGR system are that the cooler accumulates a soot, carbon and grime buildup that hampers flow and eventually requires addressing. Lack of coolant flow through the EGR cooler can cause it to rupture and the EGR valve is prone to sticking thanks to the same soot and carbon accumulation that hampers the performance of the cooler.
The Power Stroke’s First VGT
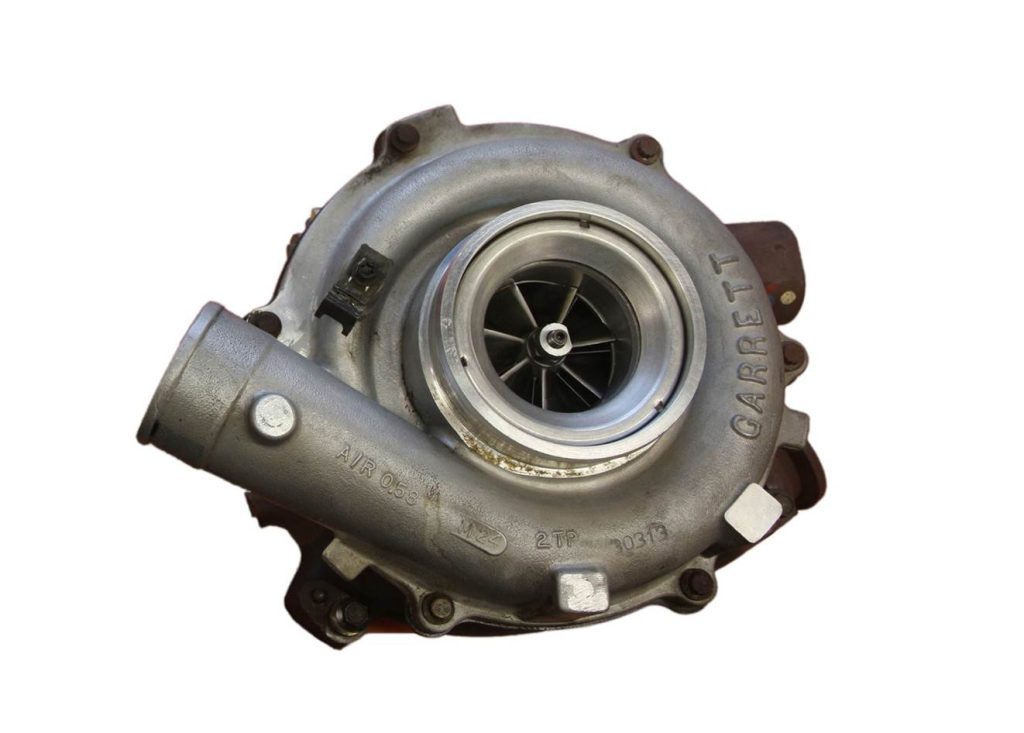
The variable geometry GT3788VA from Garrett was a rapid departure from the turbos found on the 7.3L. Vanes located within the turbine housing are electronically controlled and hydraulically actuated to alter exhaust flow across the turbine wheel for near-instantaneous response. At low rpm the vanes remain near-closed, increasing drive pressure to aid spool up. At high rpm the vanes open completely, providing for full exhaust flow. Performance of the variable geometry aspect of the turbo is commonly hindered by corrosion and/or carbon buildup on the unison ring (the metal ring that moves all vanes in concert). The GT3788VA found on ’03 engines is known for its ear-piercing whistle thanks to a 10-blade turbine wheel. The GT3788VA used on later engines utilized a 13-blade wheel that provided for quieter operation. Both VGTs are equipped with a 58mm inducer compressor wheel.
Comments (0)